What is Porosity in Welding: Crucial Tips for Achieving Flawless Welds
What is Porosity in Welding: Crucial Tips for Achieving Flawless Welds
Blog Article
Deciphering the Secret of Porosity in Welding: Tips for Minimizing Defects and Maximizing Quality
In the intricate globe of welding, porosity continues to be a consistent obstacle that can considerably influence the quality and honesty of welded joints. As we delve right into the depths of porosity in welding, discovering the keys to its prevention and control will be vital for experts looking for to grasp the art of premium weldments.
Recognizing Porosity in Welding
Porosity in welding, a typical issue experienced by welders, describes the visibility of gas pockets or spaces in the bonded product, which can compromise the stability and high quality of the weld. These gas pockets are usually trapped throughout the welding procedure due to numerous factors such as improper shielding gas, contaminated base materials, or wrong welding parameters. The formation of porosity can compromise the weld, making it susceptible to cracking and corrosion, ultimately causing structural failures.
Comprehending the source of porosity is crucial for welders to efficiently stop its incident. By identifying the importance of keeping appropriate gas shielding, ensuring the sanitation of base products, and maximizing welding settings, welders can significantly reduce the possibility of porosity development. In addition, utilizing methods like pre-heating the base product, employing correct welding strategies, and conducting thorough assessments post-welding can further help in reducing porosity problems. On the whole, an extensive understanding of porosity in welding is vital for welders to create premium and long lasting welds.
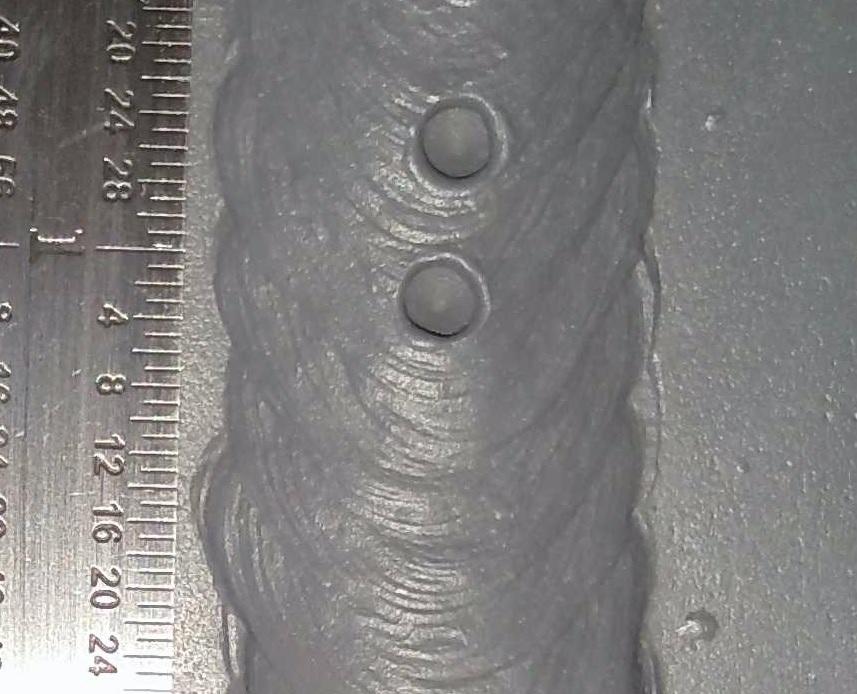
Typical Root Causes Of Porosity
When evaluating welding processes for possible high quality issues, recognizing the usual reasons for porosity is essential for keeping weld stability and protecting against architectural failings. Porosity, identified by the visibility of cavities or spaces in the weld steel, can considerably jeopardize the mechanical buildings of a bonded joint. One typical cause of porosity is improper protecting gas insurance coverage. Insufficient securing gas flow rates or incorrect gas combinations can result in atmospheric contamination, resulting in porosity development.
One more prevalent reason for porosity is the presence of dampness and impurities externally of the base steel or filler product. When welding products are not properly cleaned or are exposed to high levels of humidity, the vaporization of these pollutants throughout welding can develop voids within the weld grain. Additionally, welding at improper parameters, such as excessively high travel rates or currents, can produce excessive disturbance in the weld swimming pool, trapping gases and creating porosity. By attending to these typical reasons via correct gas securing, material prep work, and adherence to optimal welding parameters, welders can reduce porosity and boost the quality of their check here welds.
Techniques for Porosity Avoidance
Applying reliable precautionary actions is crucial in reducing the event of porosity in welding procedures. One method for porosity prevention is ensuring correct cleaning of the base steel before welding. Pollutants such as oil, oil, rust, and paint can lead to porosity, so comprehensive cleaning utilizing ideal solvents or mechanical techniques is crucial.

Making use of top notch filler products and securing gases that are ideal for the base steel and welding procedure can considerably reduce the danger of porosity. In addition, preserving proper welding parameters, such as voltage, existing, take a trip rate, and gas circulation price, is important for porosity avoidance.
Moreover, utilizing correct welding strategies, such as preserving a consistent traveling speed, electrode angle, and arc size, can aid stop porosity (What is Porosity). Ample training of welders to ensure they adhere to finest practices and quality assurance treatments is additionally vital in minimizing porosity problems in welding
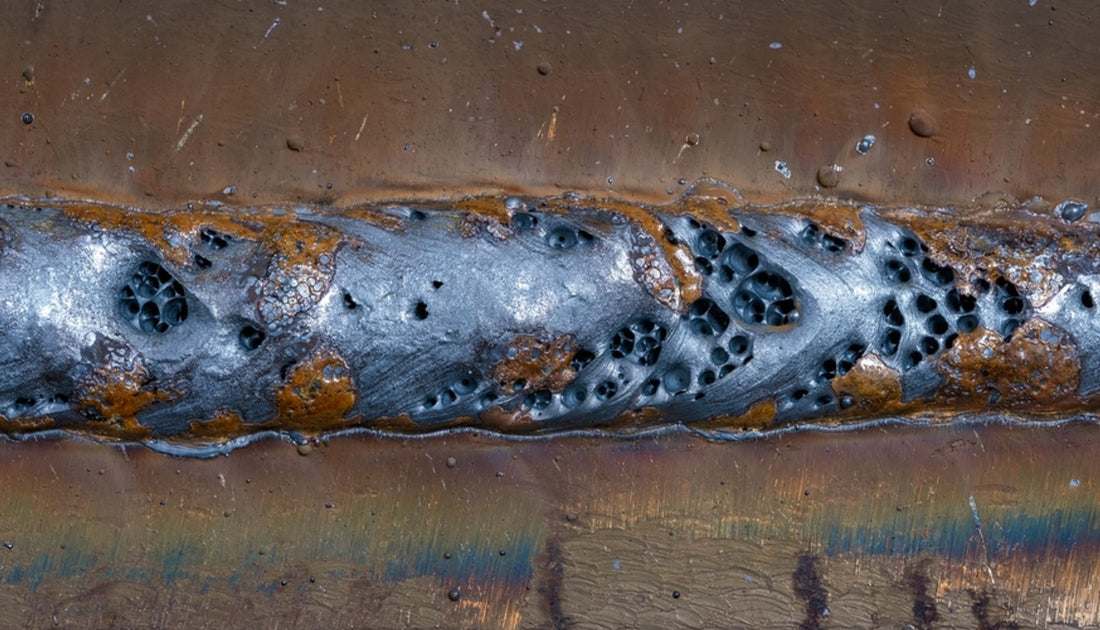
Best Practices for Top Quality Welds
One key practice is keeping correct sanitation in the welding location. Completely cleansing the workpiece and surrounding area prior to welding can assist minimize these problems.
Another ideal technique is to thoroughly pick the ideal welding parameters for the certain materials being signed up with. This includes setting the appropriate voltage, current, travel rate, and securing gas circulation rate. Proper parameter choice makes sure optimal weld infiltration, blend, and total high quality. Additionally, utilizing top quality welding consumables, such as electrodes and filler steels, can dramatically influence the last weld high quality. Spending in costs consumables can result in stronger, much more sturdy welds with less flaws. By adhering to these finest practices, welders can consistently generate top notch welds that satisfy industry standards and surpass client assumptions.
Relevance of Porosity Control
Porosity control plays a crucial role in ensuring the integrity and top quality of welding joints. Porosity, identified by the existence of tooth cavities or spaces within the weld steel, can dramatically compromise the mechanical buildings and structural honesty of the weld. Extreme porosity compromises the weld, making it more prone to fracturing, rust, and total failing under functional lots.
Reliable porosity control is crucial for keeping the preferred mechanical residential properties, such as strength, ductility, and durability, my website of the welded joint. What is Porosity. By minimizing porosity, welders can boost the general high quality and integrity of the weld, guaranteeing that it fulfills the performance needs of the desired application
Moreover, porosity control is important for accomplishing the desired aesthetic appearance of the weld. Extreme porosity not just deteriorates the weld however additionally interferes with its aesthetic charm, which can be crucial in sectors where appearances are essential. Appropriate porosity control strategies, such as using the right shielding gas, regulating the welding parameters, and guaranteeing proper cleanliness of the base products, are vital for generating premium welds with minimal defects.
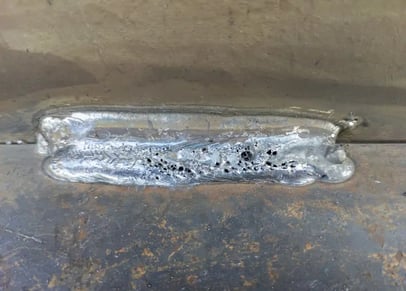
Conclusion
In conclusion, porosity in welding is a typical flaw that can compromise the top quality of the click site weld. It is necessary to regulate porosity in welding to ensure the integrity and toughness of the final item.
Report this page